K-Briq: We’ve been using the same bricks for over 5,000 years. This engineer says it’s time for a change.
Although we’re surrounded by millions of them every day, most of us don’t think about bricks too often. For thousands of years, the humble clay-fired brick hasn’t changed. The building blocks of modern suburban homes would be familiar to the city planners of ancient Babylon, the bricklayers of the Great Wall of China, or the builders of Moscow’s Saint Basil’s Cathedral.
But the brick as we know it causes significant environmental problems, by using up raw, finite materials and creating carbon emissions. That’s why Gabriela Medero, a professor of Geotechnical and Geoenvironmental Engineering at Scotland’s Heriot-Watt University, decided to reinvent it.
Originally from Brazil, Medero says she was drawn to civil engineering because it gave her passion for maths and physics a practical outlet. As she became aware of the construction industry’s sustainability issues, she started looking for solutions. With her university’s support, Medero joined forces with fellow engineer Sam Chapman and set up Kenoteq in 2009.
The company’s signature product is the K-Briq. Made from more than 90% construction waste, Medero says the K-Briq — which does not need to be fired in a kiln — produces less than a tenth of the carbon emissions of conventional bricks. With the company testing new machinery to start scaling up production, Medero hopes her bricks will help to build a more sustainable world.
The problem with Current bricks
Although they’re made from natural materials, there are problems with bricks at every step of their production.
- Bricks are made from clay — a type of soil found all over the world. Clay mining strips the land’s fertile topsoil, inhibiting plant growth.
- In conventional brick production, the clay is shaped and baked in kilns at temperatures up to 1,250°C (2,280°F). The majority of brick kilns are heated by fossil fuels, which contribute to climate change.
- Once made, bricks must be transported to construction sites, generating more carbon emissions.
- Globally, 1,500 billion bricks are produced, every year. Laid end-to-end, they would stretch to the moon and back 390 times.
- The environmental footprint of different bricks reflects multiple factors including the type of kiln, fuel, and transportation.
Enter the K-Briq.
Kenoteq, UK has launched the K-Briq – a more eco-friendly brick that is unfired and made of 90% construction waste and demolition waste. It is produced from concrete, brick, and plasterboard waste, and it’s compressed without firing. K-Briq generates less than a tenth of the carbon emissions in its manufacture than a regular brick. K-Briq looks like a normal brick, weighs the same and behaves like a clay brick, but offers better insulation properties. Bricks can produce in any color.
Earlier this year, Kenoteq won its first commission — to supply bricks for the Serpentine Pavilion 2020 in London’s Hyde Park (although the project has been postponed until summer 2021 due to the current pandemic). Designed by architectural studio Counterspace, the building will incorporate K-Briqs in grey, black and 12 shades of pink. The Pavilion’s lead architect, Sumayya Vally, says that as a recycled product, the K-Briq appealed to her. It “embodies” the past through its use of old materials, she says, adding that because the bricks can be customized, they allow “the designer to be a part of the construction process of the material,” creating unique opportunities in architecture.
Why can’t old bricks be re-used?
In the UK, around 2.5 billion new bricks are used in construction every year — and about the same number of old bricks are demolished. A seemingly simple solution to the brick production problem would be to re-use old bricks.
But it’s not that straightforward. According to Bob Geldermans, a climate design and sustainability researcher at Delft University of Technology in the Netherlands, reclaiming bricks is an expensive and “labor-intensive process.”
According to the UK’s Brick Development Association, old brick structures need to be carefully dismantled and the bricks cleaned of mortar with hammers and chisels. Reclaimed bricks are used to help renovate historic buildings or for other specialized projects but for mass construction, the process is too costly.
An additional barrier is that there’s no standardized way to check the strength, safety or durability of reclaimed bricks.
Medero says that K-Briqs could solve both these problems.
According to Medero, the K-Briq will be comparably priced to conventional bricks. Additionally, as a new product, the K-Briq has been subjected to rigorous assessment at the materials testing lab at Heriot-Watt University, and certified by BBA (British Board of Agrement). Medero claims that K-Briqs are stronger and more durable than fired clay bricks, and provide better insulation, too.
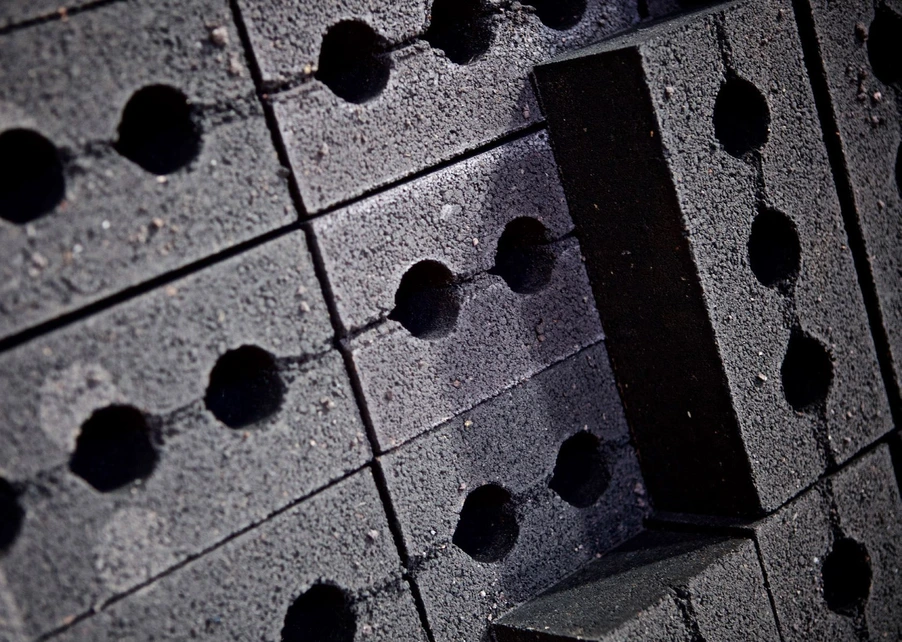
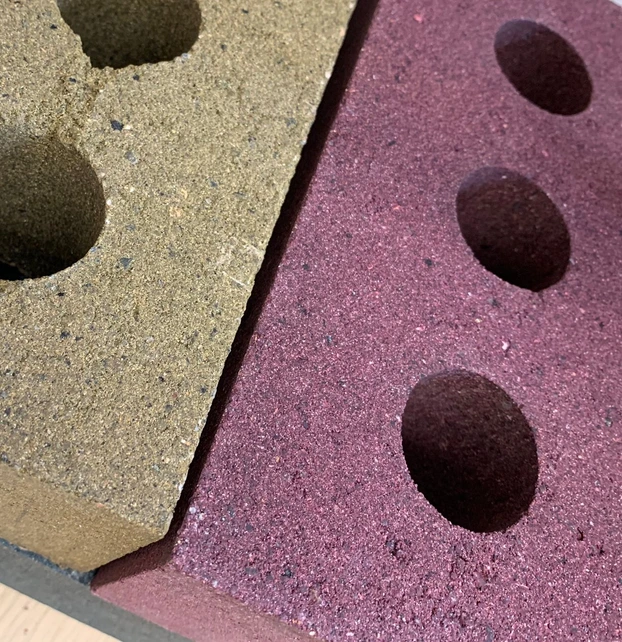
Scaling up
Kenoteq currently operates one workshop in Edinburgh, which can produce three million K-Briqs a year. Medero is looking at scaling up — but it’s hard to create a revolution in construction.
Geldermans says that the industry is notoriously slow to change — adding that legislation often lags far behind innovation.
Read Also:
- Featured Image – Source